Expert Tips for Selecting the Right Metal Stamping Services for Your Requirements
Expert Tips for Selecting the Right Metal Stamping Services for Your Requirements
Blog Article
Enhancing Performance and High Quality Via Modern Metal Stamping Approaches
In the realm of manufacturing, the mission for enhanced productivity and quality continues to be a continuous objective. Modern metal marking techniques have actually emerged as a crucial device in accomplishing these purposes, revolutionizing the sector via a blend of sophisticated modern technologies and innovative practices. As the demands for accuracy and performance proceed to escalate, the integration of automation and digital tools right into the steel marking procedure has actually become critical. The true step of success lies not only in the adoption of these modern techniques but also in the precise control of quality standards throughout the production cycle. By exploring the intricate interplay in between modern technology, automation, and accuracy in steel marking, a pathway towards unequaled efficiency and high quality assurance unfolds.
Benefits of Modern Steel Stamping
Modern metal marking offers numerous benefits in terms of performance, accuracy, and cost-effectiveness in the manufacturing sector. One of the key advantages of contemporary metal marking is its ability to successfully create high volumes of complicated metal get rid of constant top quality. This process eliminates the requirement for multiple procedures as it can carry out various jobs such as blanking, puncturing, developing, and reeling in a single operation.
In addition, contemporary metal stamping enables suppliers to achieve tight resistances and accurate requirements, ensuring that each component fulfills the required standards. This high level of precision results in minimal material waste, reduced rework, and general improved item top quality.
In addition, modern-day metal stamping is an affordable manufacturing approach. In essence, modern-day steel stamping offers an affordable edge to manufacturers looking to boost efficiency and top quality in their procedures.
Advanced Technologies in Metal Stamping
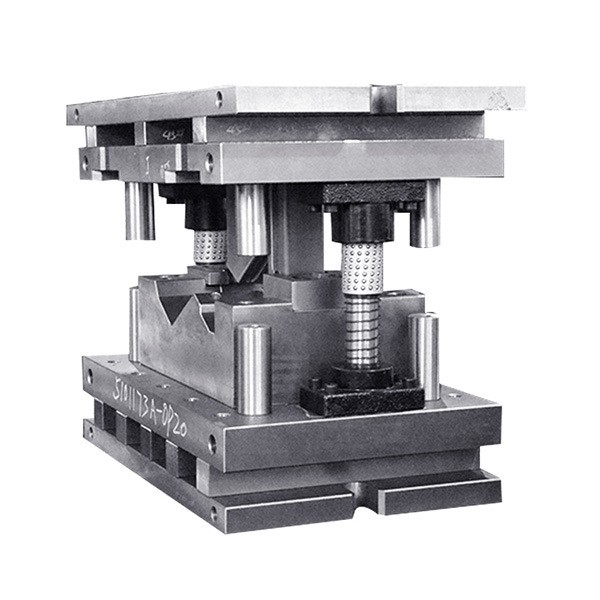
An additional vital modern technology revolutionizing steel marking is the usage of servo presses. Unlike standard mechanical presses, servo presses use higher control over the speed and force applied during the marking procedure. This control not only boosts the top quality of the stamped components but additionally minimizes product waste and energy usage.
Moreover, advancements in simulation software have actually made it possible for makers to basically test and optimize the marking procedure before physical production starts. This digital prototyping helps recognize potential concerns you can try this out at an early stage, resulting in cost financial savings and faster time-to-market for new items. Generally, these advanced modern technologies in metal stamping are driving unmatched degrees of productivity and high quality in the sector.
Improving Effectiveness Via Automation
The integration of automated systems has considerably boosted the effectiveness of steel marking processes. Automation in metal marking procedures provides a myriad of benefits, consisting of increased manufacturing rates, boosted accuracy, and minimized labor expenses. By utilizing robot arms and computer-controlled equipment, jobs that were formerly time-consuming and prone to mistakes can currently be performed promptly and with impressive accuracy.
Automated systems have the capability to deal with recurring jobs with uniformity, leading to higher productivity levels and lowered cycle times. This raised performance not just causes cost savings however additionally makes sure a much more structured and dependable manufacturing procedure. In addition, automation enables real-time surveillance and information collection, enabling producers to recognize and address issues my latest blog post immediately, further maximizing the total efficiency of steel marking operations.
Furthermore, automation promotes a more secure working atmosphere by decreasing the need for manual intervention in unsafe tasks. By delegating these obligations to automated systems, workers can focus on more complicated and value-added tasks, contributing to a much more reliable and effective workflow in the metal stamping industry.

High Quality Control Procedures in Marking
Carrying out stringent high quality control measures is vital in making certain the precision and consistency of metal stamping processes. By developing durable quality assurance methods, manufacturers can recognize and fix any kind of variances or flaws in the stamped parts, ultimately boosting product high quality and consumer complete satisfaction. One of the primary quality control measures in metal marking is performing normal examinations throughout the manufacturing cycle. These assessments entail examining the dimensions, surface area finish, and overall honesty of the stamped elements to verify compliance with the specific demands.
Furthermore, applying innovative modern technologies such as automated vision systems can even more enhance the quality assurance procedure by allowing real-time surveillance and discovery of any type of anomalies during production. These systems use electronic cameras and computer formulas to evaluate get rid of high accuracy and accuracy, minimizing the risk of flaws escaping right into the end product.
Additionally, establishing a thorough documents system that records top quality control data and examination outcomes is necessary for tracking efficiency fads and facilitating continual improvement initiatives. By assessing this data, manufacturers can determine possible locations for optimization and implement rehabilitative activities to enhance the general quality of their stamped items.
Enhancing Accuracy With Digital Tools
Utilizing electronic devices can significantly enhance the precision of steel marking procedures, revolutionizing the means suppliers accomplish precision in their production. Digital tools such as computer-aided design (CAD) software application enable the creation of elaborate stamping layouts with extremely accurate dimensions. By inputting comprehensive specs into the software, producers can ensure that each stamped item meets exact dimensional needs, reducing mistakes and waste in the production process.
Furthermore, the combination of sensing units and real-time surveillance systems in stamping equipment allows makers to carefully monitor the stamping process and make immediate modifications to guarantee specific outcomes. These digital tools offer important information on variables such as stress, speed, and alignment, permitting for quick recognition and modification of any discrepancies from the preferred specifications.
Conclusion
To conclude, imp source contemporary steel marking approaches offer many benefits for boosting performance and quality in making procedures. By utilizing advanced modern technologies, automation, quality assurance measures, and electronic devices, firms can improve effectiveness, precision, and total efficiency. These innovations in metal stamping not just enhance production procedures but likewise guarantee regular and high-grade results. Accepting these contemporary strategies can lead to considerable developments in the manufacturing industry.
Report this page